When it comes to manufacturing plastic parts, businesses and product designers often face a critical decision: Urethane Casting vs. Injection moulding. Both are popular methods, but they serve very different needs, especially when it comes to timelines, cost, volume, and flexibility. Regardless of whether you represent a startup company that wants to find rapid prototyping services or a company that wants to go into mass production, it is imperative to understand the differences between these two processes.
In this guide, we will examine the major differences, strengths, weaknesses and when each of them learn about the situation when it should be used so that you can make an informed choice in your project.
What is Urethane Casting?
Urethane casting, Low volume manufacturing. In urethane casting, plastic components are made via silicone moulds. This begins by using a master model, which is usually produced by 3D printing or CNC machining and then a mould is cast in silicone. Final parts are then made by pouring polyurethane resins into the mould.
Key Advantages:
- Low Initial Cost: There is no steep cost of manufacturing expensive steel moulds compared with injection moulding.
- Quick Turnaround: Ideal for quick prototyping, experimentation, and testing.
- Material flexibility: Covers a large range of resins with varying flexibility, hardness and colour.
- Surface Finish: Provides smooth finishes of high quality, which can be used for present or end use.
Best For:
Development of the product in its early stages
- Small-scale manufacturing (10 100 units)
- Usage of functional prototypes and design verification
What is Injection Moulding?
There is an option of making it through injection moulding, which is a mass production method of putting molten plastic into a hardened steel mould. The mould is then allowed to cool, and when cool, the part is ejected. It is the discrete industry standard to make large-scale, dependable and accurate parts.
Key Advantages:
- High Efficiency With High Volumes: The cost per unit goes down with economies of scale.
- Tight Tolerances: Suitable for involvements of complex and precision-engineered parts.
- Repeatability: Ideal set-up in case there is a mass production of similar parts.
- Material Selection: Works with a host of thermoplastics.
Best For:
- Mass production (1,000+ parts)
- High-performance, end-use parts
- Long-term production with consistent quality
Head-to-Head Comparison: Urethane Casting vs. Injection Moulding
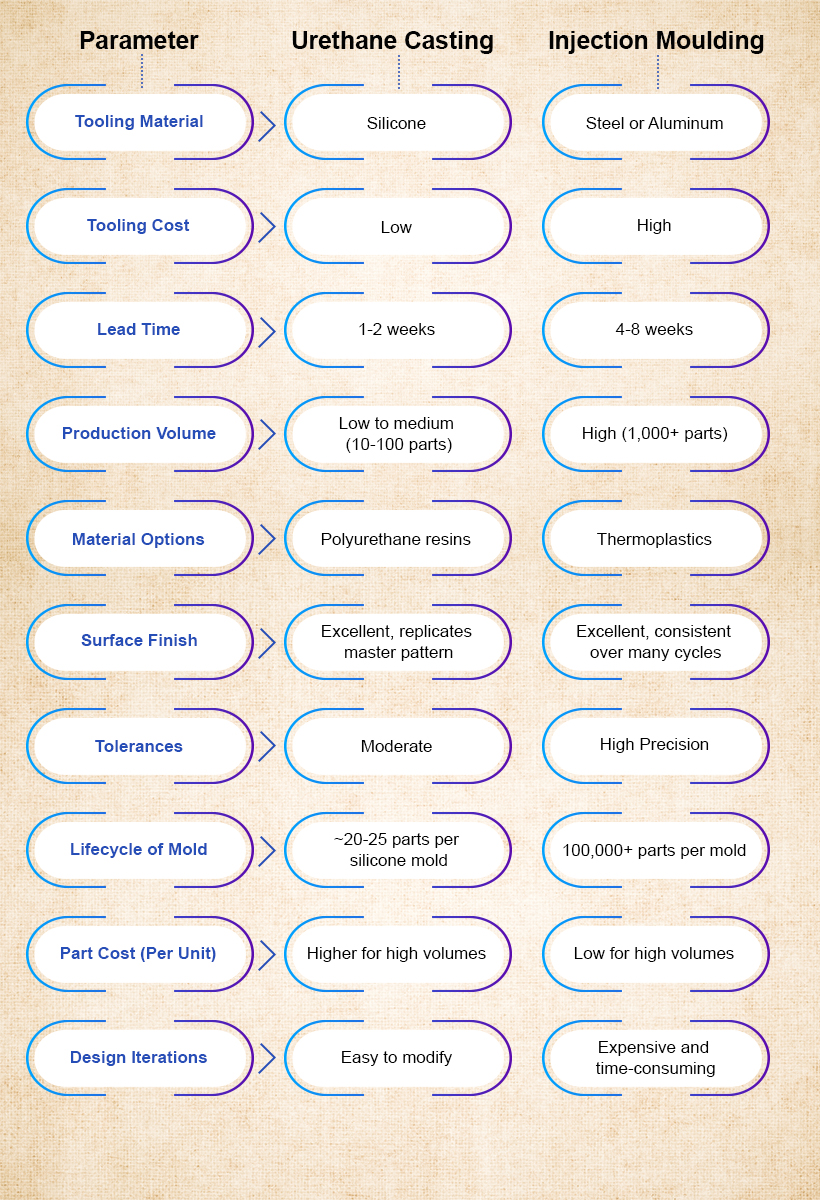
When to Choose Urethane Casting
In case you have short deadlines, small budgets, or you need to validate your design as fast as possible, urethane casting service will suit you. It provides rapid repetitions, low cost, and good cosmetic outcomes, which makes it functional to create prototypes or small production.
What Situations to Select Injection Moulding
In case you are aiming at scaling a validated product, reducing the cost per unit, and achieving durability in the future, no other manufacturing option could be as advantageous as an injection moulding service. The ROI is obvious in the case of large-scale production, though the initial expenditure might be greater.
Ending thoughts: What is better?
It does not have a one-size-fits-all answer. The question of Urethane Casting or Injection Moulding simply depends on the exact needs of your project, such as volume, cost, speed, and material expectations.
- To develop a fast iterative cycle and workable prototypes, Urethane casting takes it home.
- To produce in volume and be cost-effective, injection moulding is better.
Seeking a Good Partner?
Whether it is the reliable service of urethane casting, injection moulding service, or a stack Quick-turn rapid prototyping service provider you are looking in and around, Monarch Innovation has a precision focus and offers end-to-end support in all product development cycles that you are in a critical phase.
Partner with Monarch Innovation to bring your product to life—faster, smarter, and at scale.
FAQs
1. Which is cheaper: urethane casting or injection moulding?
Urethane casting is cheaper for low-volume production due to low tooling costs. However, injection moulding becomes more cost-effective at higher volumes (typically above 1,000 parts) because of lower per-unit costs.
2. Can urethane cast parts be used as final products?
Yes, urethane cast parts can be used as final products, especially for short production runs, market testing, or speciality applications. They offer good durability, aesthetic quality, and material flexibility.
3. How long does it take to produce parts using each method?
- Urethane Casting: 1–2 weeks from design to finished parts
- Injection Moulding: 4–8 weeks, including tooling and production setup
4. What are the limitations of urethane casting?
- Limited mould life (~20–25 parts per silicone mould)
- Manual process not suitable for high volumes
- Material properties may not fully match engineered thermoplastics
5. Which process is better for rapid prototyping?
Urethane casting is better for rapid prototyping due to its quick setup, lower cost, and design flexibility. It allows for fast iterations without heavy investment in tooling.