Design for Additive Manufacturing

Design for Additive Manufacturing Services
In the ever-evolving landscape of manufacturing, Design for Additive Manufacturing (DFAM) has emerged as a game-changer. Unlike traditional manufacturing methods that impose numerous constraints, DFAM enables engineers and designers to explore innovative geometries, optimize material usage, and enhance product performance. By harnessing the power of additive manufacturing (AM), businesses can achieve greater design flexibility, reduce waste, and accelerate product development.
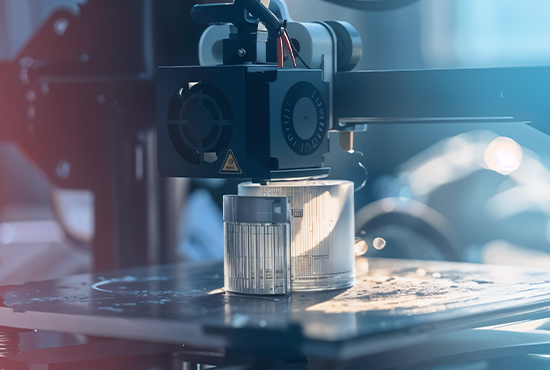
Enhancing Product Development with Early-Stage DFAM Integration

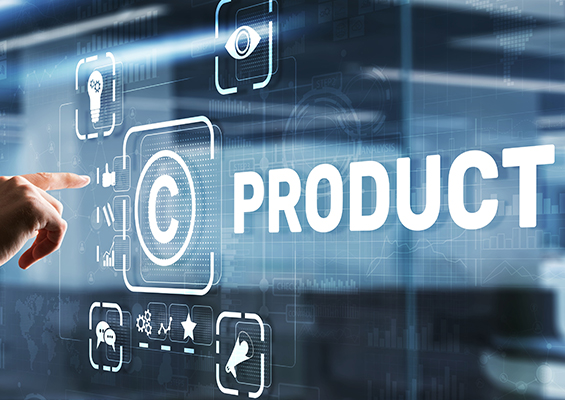
A key aspect of Design for Additive Manufacturing (DFAM) is integrating 3D printing considerations right from the initial design phase. Unlike traditional manufacturing, which relies on subtractive or formative processes like machining, molding, and casting—each with its own set of limitations—additive manufacturing (AM) builds products layer by layer, unlocking new possibilities in design complexity and material efficiency.
At Monarch Innovation, we prioritize early-stage DFAM integration to help businesses maximize the advantages of 3D printing, ensuring:
- Optimized Part Geometry – Eliminates unnecessary bulk while maintaining structural integrity.
- Material Efficiency – Enables engineers to choose the ideal material for strength, flexibility, and durability.
- Cost Reduction – Minimizes design iterations and post-processing, leading to greater efficiency.
- Customization & Complexity – Allows for the seamless realization of intricate designs that were previously impossible.
By leveraging advanced DFAM strategies, Monarch Innovation empowers businesses to streamline production, reduce waste, and push the boundaries of design innovation. Whether you’re developing lightweight aerospace components, high-performance automotive parts, or customized medical devices, our expertise ensures that your products are designed for success from the start.
Mechanical Differences Between DfAM and DFM
Design for Additive Manufacturing (DFAM) and Design for Manufacturing (DFM) differ significantly in their approach, constraints, and mechanical considerations due to the fundamental differences between additive and traditional manufacturing methods.
Manufacturing Process
- DFM: Uses subtractive/formative processes (machining, molding) with tooling constraints.
- DFAM: Builds parts layer by layer, enabling complex geometries.
Structural Design
- DFM:Requires uniform walls, simple cuts, and tool access.
- DFAM: Allows lattice structures, variable thickness, and organic shapes.
Material Efficiency
- DFM:Wastes material due to cutting/milling.
- DFAM:Minimizes waste by using only necessary material.
Assembly & Part Consolidation
- DFM: Requires multiple parts and fasteners.
- DFAM:Enables single-piece, integrated designs.
Mechanical Properties
- DFM: Isotropic materials with uniform strength.
- DFAM: Anisotropic properties based on printing direction, requiring strategic design.
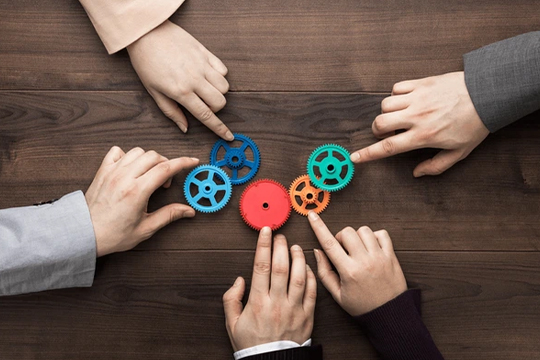
By leveraging advanced DFAM strategies, Monarch Innovation empowers businesses to streamline production, reduce waste, and push the boundaries of design innovation. Whether you’re developing lightweight aerospace components, high-performance automotive parts, or customized medical devices, our expertise ensures that your products are designed for success from the start.
Partner with Monarch Innovation and redefine what’s possible with additive manufacturing!
No Tooling, No Setup Costs: The Advantage of DFAM
One of the most significant advantages of additive manufacturing is eliminating the need for expensive molds and setup. Traditional manufacturing processes often require costly tooling, which is not only time-consuming but also adds to the overall production expense. DFAM at Monarch Innovation ensures:
No Tooling Required
- No Tooling Required – Unlike traditional machining, casting, or molding, AM doesn’t need expensive dies, molds, or fixtures, reducing upfront investment.
- Minimal Setup Costs – Traditional manufacturing requires retooling and setup for each production run, while AM enables on-demand production with minimal preparation.
- Faster Iterations – Design changes can be implemented quickly without modifying expensive tooling, making prototyping and customization more cost-effective.
- Cost Savings for Low-Volume Production – DFAM is ideal for small-batch or custom parts, eliminating the high costs associated with traditional mass production.
By removing these constraints, DFAM enables greater design freedom, faster development, and cost-efficient production—perfect for aerospace, healthcare, and automotive innovation.
The Economics of Additive Manufacturing vs. Traditional Manufacturing
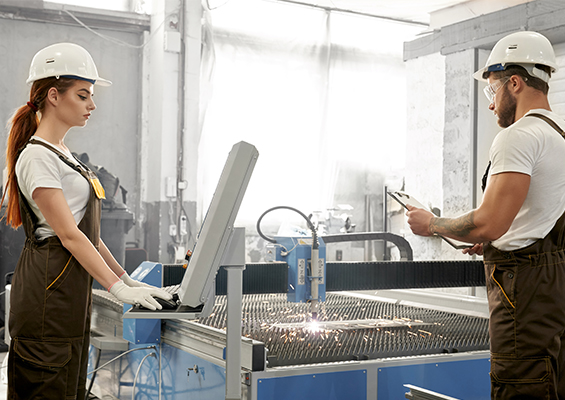
Understanding the economic impact of DFAM manufacturing versus traditional methods is crucial for businesses looking to optimize costs. While traditional manufacturing excels in mass production due to economies of scale, additive manufacturing provides distinct financial benefits in several areas:
Cost Comparison:
Factor | Traditional Manufacturing | Additive Manufacturing |
Setup & Tooling Costs | High | None |
Material Wastage | High (subtractive) | Minimal (additive) |
Customization | Limited | High |
Lead Time | Weeks to months | Days to weeks |
Production Efficiency | High for large volumes | Best for custom/small batches |
For businesses that require on-demand, customized solutions, DFAM service at Monarch Innovation offers a financially viable alternative that accelerates time-to-market while maintaining high-quality production.
On-Demand Manufacturing with 3D Printing
On-demand manufacturing powered by 3D printing eliminates the need for mass production and large inventories, offering a more flexible, cost-effective, and efficient approach to manufacturing.
- No Inventory Costs – Produce parts only when needed, reducing storage and warehousing expenses.
- Faster Time-to-Market – Quickly manufacture prototypes or final products without long lead times.
- Customization & Flexibility – Easily modify designs for personalized or small-batch production.
- Reduced Waste – Uses only the required material, making production more sustainable.
- Supply Chain Resilience – Minimize dependence on global supply chains with localized, on-demand production.
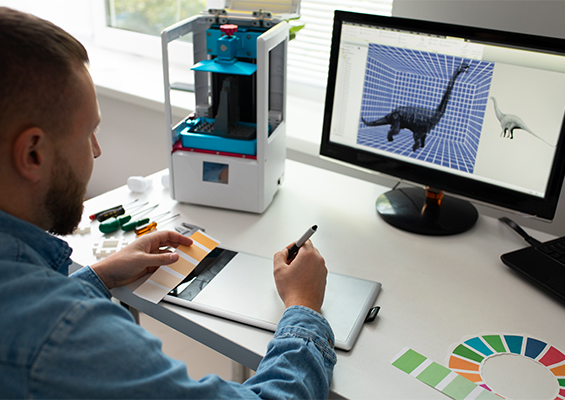
Additive Manufacturing Services for Your Business
Unlock the full potential of 3D printing with our Additive Manufacturing (AM) services, designed to enhance efficiency, flexibility, and innovation in your production process.
Our Services
- DFAM (Design for Additive Manufacturing) – Optimize designs for lightweight, high-strength, and complex geometries.
- Rapid Prototyping – Develop and test prototypes quickly and cost-effectively.
- Low-Volume & Custom Production – Manufacture parts on-demand without high tooling costs.
- Material & Process Selection – Choose from plastics, metals, and composites for the best performance.
- Post-Processing & Finishing – Enhance surface quality and mechanical properties with specialized treatments.
Connect with us for all your Engineering design needs
Address
3rd Floor, Dwarkesh Business Hub,
Opp.Home Town, Motera,
Ahmedabad-380005, GJ, India